Moving the 1100-foot long truss span to set up a detour bridge was another milestone in the effort to replace Multnomah County’s 87-year old Sellwood Bridge. The truss span was moved on Saturday, January 19, 2013. Moving it north created space for the new Sellwood Bridge to be built in the alignment of the old bridge.
The 3400-ton truss span was one of the longest bridge parts ever moved. The age and shape of the truss combined with the curved path of the move made it a highly complex undertaking.
Setting up the detour bridge required the Sellwood Bridge to be closed to all users – motorists, pedestrians and bicyclists – from January 17 to January 23. Originally, the project team had planned for the bridge to be closed until January 24, but it opened one day early after a successful move.
The actual move only took about 14 hours, but the extra closure days were needed to install road connections at each end of the truss span and complete an in-depth inspection of the detour bridge before it opened to traffic. The detour bridge is now carrying motorists, bicyclists and pedestrians across the river until the new Sellwood Bridge opens in the summer of 2015.
Bridge Move Explained
Thanks to Multnomah County Engineer Ed Wortman for the following summary describing the bridge move.
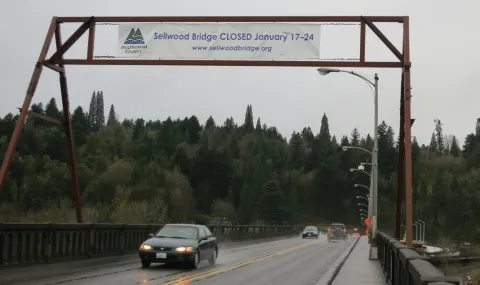
Sellwood’s Steel Truss Span
- The existing steel truss span was a continuous structure about 1100 feet long.
- The structure was a four-span continuous truss. The steel structure consisted of four spans between support piers but was continuous over the entire 1100-foot length with no hinges or expansion joints.
- Four-span continuous trusses are exceedingly rare. We’re aware of only a couple of others in the United States. Sellwood’s designer, Gustav Lindenthal (world-famous bridge engineer from New York), chose a continuous truss design to minimize the amount of steel. A small budget required an economical design.
- In its original position the truss was supported on five concrete piers, three in the river and two at the east and west shorelines. Lengths of the four spans from west to east were about 245 feet, 300 feet, 300 feet and 246 feet.
- At each of the five piers, the truss was supported on two large steel bearings, with one bearing under the north side of the truss and one under the south side.
The individual parts of the steel truss were fabricated in 1924 at Judson Manufacturing Company in Emeryville, California. Sellwood was one of the first large steel bridges in the Portland area that was fabricated on the West Coast. Steel bridges older than Sellwood were generally fabricated in Pennsylvania or other eastern states.
Overhead view of existing and detour bridge alignments
Why Move the Truss?
- The Sellwood truss was moved (or “translated,” as engineers and construction crews say) sideways to a new location north of the existing bridge to serve as a temporary detour structure while the new Sellwood Bridge was built at the original bridge location.
- At the new location, the truss was supported on five temporary steel “bents” or piers. The contractor installed the new bents at the same spacings as the existing concrete piers. The new bents supported the truss at the same 10 bearing points (two per bent) where the original concrete piers supported it.
- The entire 1100-foot long, four-span truss was moved sideways to its new location as a single unit. The bridge was moved in a horizontal slide, rather than a vertical pick-and-move.
- While translation of shorter bridges is quite common, it is highly unusual to translate a multi-span bridge of this length in one piece. Considering the rarity of four-span bridges, the Sellwood move could be the first time such an operation has been performed for a structure of this type. Comparisons with similar projects have been difficult to find.
- Due to the necessary locations of the temporary east and west approaches to the detour bridge, the location of the truss after its move is at a “skew” to its original alignment. The east end of the truss moved north about 33 feet and the west end moved north about 66 feet. This means that the truss traveled along a curved path as it was translated.
Who Moved the Truss Span?
- The translation operation was carried out by two contractors working together: the Slayden/Sundt Joint Venture and Omega Morgan. Omega Morgan is an Oregon subcontractor that worked for Slayden/Sundt.
- The Slayden/Sundt Joint Venture was Construction Manager/General Contractor (CMGC) for the entire Sellwood Bridge replacement project. The joint venture consists of Slayden, a Stayton, Oregon-based heavy construction contractor, and Sundt, an Arizona-based general contractor.
- Slayden/Sundt (SSJV) had overall responsibility for the translation operation and performed portions of the translation-related work with their own crews and equipment.
Omega Morgan is a Hillsboro-based contractor involved in transporting and handling heavy equipment and structures. As a subcontractor, Omega Morgan provided specialized equipment for the translation and planned and directed the translation operation.
Cross section view of existing and detour bridge piers and translation beam
Methods and Equipment
- Since the truss span is continuous over its full 1100-foot length, it was important to support the truss at its 10 main bearing points (two per pier) throughout the move. Otherwise the load-carrying capacity of truss parts could have been exceeded.
- To support the truss at all 10 bearing points during translation, the contractor installed steel “translation beams” from the five old concrete piers to the five new temporary steel piers.
- Two translation beams were used at each pier to accommodate Omega Morgan’s “skidding” (or sliding) equipment. One translation beam was positioned on either side (east and west) of the bearings that support the truss on the piers.
- Omega Morgan’s equipment lifted the truss off the concrete piers, then slid the truss along the translation beams to the steel temporary bents. Hydraulic jacks pushed the truss on its journey. Omega Morgan has used this equipment regularly for operations such as moving newly-built barges at the Port of Portland and loading container cranes onto barges at ports. Some of the same equipment was used to load the arch span for the new Sauvie Island Bridge onto a barge in 2007 in preparation for moving it to the bridge site.
- To prepare for the truss-sliding operation, Omega Morgan first installed U-shaped “track beams” on top of the translation beams from the concrete piers to the steel bents. Teflon pads were glued to the track beams to provide slick sliding surfaces.
- To actually lift and slide the bridge truss, Omega Morgan used their standard “skid beams.” The skid beams were 14-foot long ski-shaped steel units that slid on the Teflon pads in the track beams. Four skid beams were used at each of the concrete piers, with two of the skid beams located at the north side bridge bearing and two at the south side bearing. At each bridge bearing, the two skid beams sat on the track beams on the east and west sides of the bearing.
- For the Sellwood operation, each skid beam had two vertically-oriented 150-ton capacity hydraulic jacks for lifting the truss off the concrete piers and lowering it onto the temporary steel piers. With two skid beams at each bearing, this meant that four jacks lifted the truss at each bearing.
Since there were 10 bearings in total (two per pier), 40 jacks were used to lift the truss. At each of the three river piers, the weight of the truss (including concrete roadway deck) was about 900 tons. At each of the end piers, the bridge weight was about 340 tons. The total weight of the truss span was estimated to be about 3400 tons.
Cross section of jacking system supporting truss span - In preparation for the lifting and translation operations, the contractor installed custom-designed steel “cradles” at each truss bearing (10 cradles total). The cradles carried the weight of the truss from the bearing to the four lifting jacks.
- To move the skid beams and truss along the track beams, Omega Morgan used 10 horizontally-oriented 75-ton capacity hydraulic jacks to push on the south side skid beams. The north skid beams and south skid beams were tied together to assure that they moved together.
- The pushing jacks were pinned to the rear ends of the skid beams and pushed against clips on the sides on the track beams. Due to the slick surface provided by the Teflon pads in the track beams, only a small part of the pushing jack capacity was needed to move the truss. The pushing jacks could also have been used to pull back in case a skid beam moved too far.
- The truss moved along a curved path due to the skewed alignment of the detour bridge relative to the original bridge. The steel translation beams were designed to account for this curve. The truss shifted sideways about 33 feet northward at the east end and 66 feet at the west end.
- To move the truss along the curved path, Omega Morgan controlled the pushing jacks such that the jacks at the west end pushed twice as fast as the east end jacks, with the jacks at the other three points pushing at proportional rates. To accomplish this, Omega Morgan used a “digitally-controlled power pack” that controlled the amount of hydraulic fluid going to each jack.
Monitoring the Move
The truss moved at different rates along each of the translation beam pairs in order to move on a curved path. Omega Morgan and the general contractor monitored the progress of the truss in two ways:
- With marks on the translation beams or track beams. Before translation started, each beam was marked to show how far the truss had progressed at any given point in time. During translation, Omega Morgan stopped moving the truss periodically to allow staff to determine the truss location on each beam. The actual locations were compared to figures on an “offset table” to make sure the truss was moving at the desired rate at each beam.
- A surveying subcontractor on land monitored locations of targets at the bearing points on the truss.
Additional Monitoring for the Truss
The Sellwood truss was a long, slender structure with a finite amount of inherent strength. Truss members could have been damaged if the truss was bent or twisted excessively during translation. A number of measures were taken to minimize the potential for damage:
- An engineering firm on the County’s team analyzed the truss to see how much it could be bent or twisted without causing damage. Based on results of the analysis, “tolerance limits” were established for the permissible amount of deformation from vertical bending, horizontal bending and twist.
- During translation, the contractor team used three methods to check the amount of deformation in the truss:
- Marks on the translation beams or track beams as described above. The contractor team periodically checked the actual location of the truss along the beams against numbers on the “offset table” to see if the truss was within tolerance for sideways bending.
- Laser instruments attached to the truss itself with laser beams aligned along the truss. The contractor monitored the laser beams at each truss support point to make sure the truss stayed in a straight line up and down as well as sideways.
- Visual surveying by a subcontractor with an instrument set up on shore. The survey program mentioned above provided data on truss shape as well as on truss location.
- In addition to deformation checks by the contractor team, Multnomah County staff also did the following:
- GPS surveying by a County engineering team.
- Strain gauge measurements on truss members. A local engineering firm specializing in monitoring stresses in bridges and other structures installed electrical strain gauges on critical truss members. These gauges measured deformations in the members during translation. Engineers on the County team set limits on the amount of allowable strain.
Attaching the Truss to the Detour Bridge Piers
Once the truss reached its final location over the detour bridge piers, the span was lowered about two inches onto temporary bearings. The 150-ton vertical jacks on the skid beams were used to lower the truss span. The temporary bearings were steel plates installed at the correct heights to support the truss span.
At Detour Bridge Pier 19 (in the center of the truss and river), steel guide bars attached to the pier top bearings surrounded the truss bearings to keep them from moving in any direction. At the other four temporary piers, the truss bearings were held in place with guide bars on the north and south sides but are allowed to slide back and forth in the east/west direction as the truss expands and contracts due to temperature changes. To allow the truss bearings to slide freely on the pier top bearings, Teflon pads ride on stainless steel sheets between the bearing surfaces.
The old Sellwood Bridge was also designed to allow for this natural expansion and contraction of several inches. For the old bridge, steel rockers were used to allow east/west movement rather than Teflon pads.
Safety Inspection After the Move
Immediately after the translation was completed and before public traffic was allowed on the truss, a team of experienced bridge inspectors from a Northwest consulting firm inspected the structure to see if any damage occurred during the move. This inspector team was very familiar with the Sellwood truss since they had inspected it numerous times over the years, including a “pre-translation” inspection to establish a baseline for the post-translation inspection.